Addressing Valve Leakage: Causes, Prevention, and Solutions
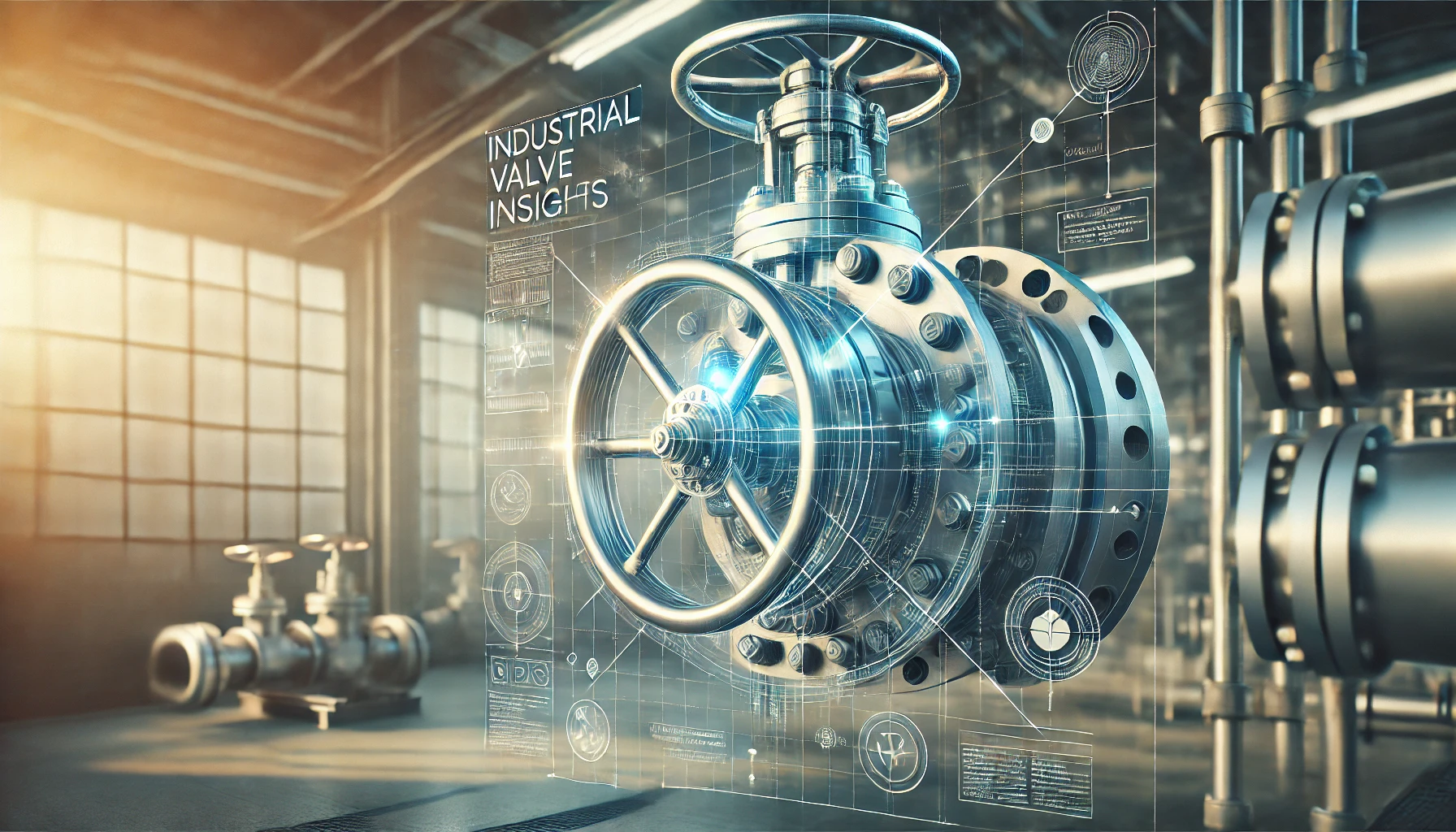
Introduction to Valve Leakage
Definition and significance of valve leakage
Valve leakage refers to the unwanted flow of fluid through the valve when it is intended to be closed. This leakage can occur in various types of valves, including ball valves, gate valves, and globe valves. The significance of valve leakage lies in the potential for costly consequences, such as the loss of valuable fluids, contamination of processes, and compromised safety.
Understanding the potential consequences of valve leakage
Valve leakage can lead to a wide range of negative consequences. For instance, in industrial settings, it can lead to the loss of valuable chemical substances or other fluids, resulting in monetary losses. Additionally, if the leaked fluid is hazardous or toxic, it can pose serious health and safety risks to personnel and the environment. Valve leakage can also impact the efficiency and reliability of operations, leading to decreased productivity and suboptimal performance.
### Importance of addressing valve leakage promptly
Addressing valve leakage promptly is crucial to mitigate the potentially adverse effects. Failure to take appropriate action can lead to further damage to the valve and surrounding equipment, as well as escalate the costs associated with repair or replacement. Moreover, neglecting valve leakage can compromise the overall integrity and safety of the system, posing long-term risks and hazards.
Causes of Valve Leakage
Wear and Tear
1. Age-related degradation of valve components
Valves, like any mechanical device, are subject to wear and tear with prolonged use. Over time, the moving parts, such as the stem, ball, or disc, can experience deterioration, resulting in gaps or irregularities that allow fluid to pass through. The deterioration of seals and gaskets also contributes to valve leakage.
2. Effects of corrosion and erosion on valve performance
Corrosive fluids and abrasive particles present in the process media can erode or corrode valve surfaces, leading to leakage. Corrosion weakens the materials, while erosion removes material, compromising the valve’s integrity.
3. Role of mechanical stress and fatigue on valve leakage
Valves are often subjected to mechanical stress from factors like pressure differentials, vibration, or frequent operation. This stress can cause fatigue in the valve components over time, resulting in cracks or deformations that allow leakage.
### Improper Installation and Maintenance
1. Impact of incorrect installation or insufficient tightening
Improper installation, such as incorrect alignment or inadequate tightening of bolts, can create gaps or misalignments that lead to valve leakage. Inadequate tightening can also cause gaskets to deform or fail, resulting in leaks.
2. Neglecting regular maintenance and inspection procedures
Failure to conduct regular maintenance and inspections can allow small issues, like worn seals or loose connections, to go unnoticed and develop into significant leakage problems. Regular maintenance and inspection help identify and address potential sources of leaks before they worsen.
3. Inadequate lubrication and lack of cleanliness
Proper lubrication is essential for the smooth operation of valve components and preventing leaks. Inadequate lubrication can lead to increased friction, wear, and ultimately, valve leakage. Additionally, a lack of cleanliness, such as the presence of debris or contaminants, can interfere with the valve’s sealing surfaces and cause leakage.
### Sealing and Gasket Issues
1. The importance of proper sealing materials and techniques
Choosing the right sealing materials and employing proper sealing techniques is critical to preventing valve leakage. The wrong choice of materials that do not withstand the process conditions, or improper sealing techniques that result in incomplete contact between sealing surfaces, can lead to leaks.
2. Common causes of gasket failure and leaks
Gasket failure is a common cause of valve leakage. Gaskets can fail due to factors such as deterioration, improper installation, excessive compression, or exposure to extremes in temperature or pressure.
3. How temperature, pressure, and chemical compatibility affect sealing efficiency
Temperature, pressure, and chemical compatibility greatly influence the efficiency of valve sealing. Extreme temperature variations can cause seals to expand or contract, compromising their ability to create a tight seal. High pressures can exceed the capabilities of the sealing materials, resulting in leaks. Chemical incompatibility can cause the degradation or swelling of gaskets and seals, leading to leakage.
### Process-related Factors
1. Influence of fluid properties on valve leakage
The fluid properties, such as viscosity, corrosiveness, and presence of solid particles, can impact valve performance and contribute to leakage. Highly viscous fluids may hinder the valve’s ability to close tightly, while corrosive fluids can erode valve surfaces, creating leak paths. Solid particles can also cause wear and damage to valve components, leading to leaks.
2. Effects of extreme temperatures and pressure differentials
Extreme temperatures or significant pressure differentials can exert excessive stress on valve components, causing them to warp, crack, or deform. These conditions can create leak paths through which fluid can escape.
3. How cavitation and flashing contribute to valve leakage
Cavitation and flashing are phenomena that can contribute to valve leakage. Cavitation occurs when the fluid pressure drops below its vapor pressure, causing the formation and collapse of bubbles that can erode surfaces and promote leakage. Flashing occurs when a high-pressure liquid rapidly changes to a vapor, leading to a sudden drop in pressure and the potential for leaks.
### Manufacturing Defects
1. Recognizing flaws in valve components
Manufacturing defects in valve components can be a significant cause of valve leakage. Flaws in casting, machining, or assembly processes can create irregularities or weak points that allow fluid to pass through.
2. The impact of inadequate quality control measures
Inadequate quality control measures during the manufacturing process can result in substandard valve components that are prone to leakage. Insufficient inspections, lack of adherence to engineering specifications, or inadequate testing can all contribute to the prevalence of manufacturing defects.
3. Understanding the prevalence of manufacturing defects
While stringent quality control measures aim to minimize manufacturing defects, their prevalence cannot be completely eliminated. Small imperfections or errors in the manufacturing process can go undetected, resulting in valves with latent leakage issues.
## Prevention Measures for Valve Leakage
### Regular Inspection and Maintenance
1. Establishing a comprehensive maintenance schedule
Implementing a comprehensive maintenance schedule is crucial to preventing valve leakage. Regular inspections, cleaning, and lubrication help identify and address any potential sources of leaks in a timely manner, ensuring the optimal performance and longevity of the valve.
2. Importance of proactive valve condition monitoring
Proactive valve condition monitoring involves utilizing advanced techniques such as vibration analysis, acoustic monitoring, or thermal imaging to detect early signs of potential valve failure or leakage. By identifying issues before they escalate, proactive monitoring helps reduce the risk of significant leaks.
3. Implementing preventive maintenance techniques
Preventive maintenance techniques, such as valve exercising, re-torquing bolts, or replacing worn seals and gaskets, can significantly reduce the likelihood of valve leakage. These proactive measures help address wear and tear, equipment degradation, and potential sources of leaks before they become major problems.
Proper Installation and Training
1. Adhering to manufacturer guidelines for installation
Following the manufacturer’s guidelines for installation is crucial to ensure the proper functioning and sealing of valves. Proper alignment, sufficient tightening of bolts, and correct torque values are essential for preventing leaks.
2. Importance of competent and trained personnel
Ensuring that personnel involved in valve installation, maintenance, and inspection are competent and properly trained is vital. Proper training can enhance their understanding of valve components, correct installation procedures, and the importance of adherence to proper maintenance protocols, reducing the likelihood of valve leakage.
3. Ensuring proper torque and alignment during installation
Proper torque and alignment during installation are critical for achieving a secure seal and minimizing the risk of leakage. Using torque wrenches and alignment tools can help ensure the correct application of torque and alignment specifications, providing a reliable seal.
### Material Selection and Design Considerations
1. Choosing appropriate materials with excellent corrosion resistance
Selecting materials with excellent corrosion resistance is crucial for preventing valve leakage. Considering the compatibility of materials with the process media, including resistance to corrosive substances, is essential to maintain the integrity of valves over their lifespan.
2. Role of engineering design to prevent leakage
Engineering design plays a significant role in preventing valve leakage. Design considerations, such as proper sealing surfaces, adequate reinforcement of critical areas, and robust construction, help minimize potential leak paths and ensure the reliability of the valve.
3. Identifying potential weak points in valve design and improving them
Identifying potential weak points in valve designs, such as areas prone to erosion, inadequate sealing, or stress concentration, allows for their improvement. Reinforcing these weak points through engineering design modifications minimizes the risk of leakage and enhances the overall performance of the valve.
### Secure Sealing Techniques
1. Utilizing proper gaskets and seals for specific applications
Selecting the appropriate gaskets and seals for specific applications is vital to ensuring effective sealing and preventing leaks. Different types of gaskets, such as spiral wound, graphite, or elastomer-based seals, offer varying levels of resistance to temperature, pressure, and chemical compatibility.
2. Implementing procedures for correct gasket installation
Correct gasket installation procedures are essential for achieving a secure seal and preventing leakage. Techniques such as proper surface preparation, correct gasket positioning, and the use of appropriate sealants or lubricants can enhance the sealing efficiency and reliability of valves.
3. Importance of regular inspection and replacement of worn-out seals
Regular inspection and timely replacement of worn-out seals are essential preventive measures against valve leakage. Monitoring the condition of seals and replacing them when signs of wear or damage are detected ensure that the valve remains properly sealed and minimizes the risk of leaks.
### Testing and Quality Control
1. Incorporating rigorous testing procedures during manufacturing
Incorporating rigorous testing procedures during the manufacturing process is critical to ensuring the quality and integrity of valves. Testing methods such as hydrostatic testing, leak testing, or performance testing help identify any potential leaks or defects, enabling corrective actions before the valves reach the end-users.
2. Proper documentation of quality control measures
Proper documentation of quality control measures during the manufacturing process is crucial to ensure traceability and adherence to specifications. Documenting testing procedures, inspection results, and compliance with industry standards allows for accountability and reliable quality control.
3. Independent validation and third-party inspections
Independent validation and third-party inspections add an extra layer of quality assurance. Collaborating with reputable organizations or independent inspectors for impartial validation can help identify any potential shortcomings in the manufacturing process and contribute to the prevention of valve leakage.
## Effective Solutions for Valve Leakage
### Repair vs. Replacement Considerations
1. Evaluating the condition and severity of valve leakage
When addressing valve leakage, evaluating the condition and severity of the leak is crucial in determining the most effective solution. Factors such as the extent of leakage, the age of the valve, and the availability of spare parts influence the decision between repair or replacement.
2. Balancing cost and benefits of repair and replacement options
Balancing the cost and benefits of repair and replacement options is essential in determining the most economical solution. Factors such as repair costs, downtime, and the long-term reliability of the valve should be considered to optimize cost-effectiveness.
3. Factors influencing the decision-making process
Several factors can influence the decision-making process when addressing valve leakage. These include the severity of the leakage, the age of the valve, the availability of spare parts, the impact on operations, and the associated costs. A thorough analysis of these factors helps in making an informed decision.
### Valve Maintenance Best Practices
1. Effective methods for cleaning and lubrication
Proper cleaning and lubrication are essential maintenance practices for preventing valve leakage. Using suitable solvents or cleaning agents to remove dirt, debris, or deposits ensures unimpeded valve operation. Additionally, applying appropriate lubricants to reduce friction and enhance sealing efficiency promotes optimal valve performance.
2. The role of preventive maintenance in avoiding leaks
Implementing preventive maintenance measures plays a significant role in avoiding valve leaks. Regular inspections, cleaning, lubrication, and component replacements, based on predetermined schedules or condition-based monitoring, help detect and rectify potential leak sources before they become significant issues.
3. Proven techniques for extending valve lifespan
Extending the lifespan of valves reduces the likelihood of leakage. Techniques such as condition-based maintenance, routine testing, and the use of technology-enabled predictive maintenance help identify and address potential issues at an early stage, maximizing the valve’s longevity and preventing leaks.
### Advanced Technologies and Innovations
1. Introduction to smart valve monitoring systems
The introduction of smart valve monitoring systems revolutionizes valve maintenance and leakage prevention. These systems utilize sensors and data analytics to monitor valve performance, detect anomalies, and provide real-time insights. By enabling predictive maintenance, they help identify and address potential sources of leakage before they escalate.
2. Utilizing real-time data for predictive maintenance
Real-time data provided by smart valve monitoring systems offers valuable insights for predictive maintenance. Analyzing data on factors such as pressure, temperature, flow rate, and vibration helps predict and prevent potential valve leakage, optimizing maintenance schedules and reducing downtime.
3. Emergence of leak detection technologies and their benefits
The emergence of advanced leak detection technologies contributes significantly to the prevention of valve leakage. Innovations such as acoustic leak detection systems, infrared imaging, or ultrasonic examination provide efficient methods for early leak detection, facilitating prompt repairs and preventing further damage.
### Collaboration and Industry Standards
1. Importance of partnering with reliable valve suppliers and manufacturers
Partnering with reliable valve suppliers and manufacturers is crucial for addressing valve leakage effectively. Establishing trusted relationships ensures access to high-quality valves, proper guidance for installation and maintenance, and reliable after-sales support.
2. Understanding industry regulations and standards
Having a comprehensive understanding of industry regulations and standards is vital for preventing valve leakage. Compliance with regulations related to safety, environmental protection, and product quality ensures that valves are designed, manufactured, and used to meet the necessary standards for leak prevention.
3. Promoting knowledge exchange to address valve leakage collectively
Promoting knowledge exchange and collaboration within the valve industry is essential for collectively addressing valve leakage. Sharing best practices, research, and experiences helps identify innovative solutions, improve industry standards, and facilitate continuous improvement in leak prevention.
*Summary and FAQs
*Summary of key points discussed in the article
Throughout this article, we have explored the causes, prevention measures, and effective solutions for valve leakage. Valve leakage can result from wear and tear, improper installation and maintenance, sealing and gasket issues, process-related factors, and manufacturing defects. To prevent valve leakage, regular inspection and maintenance, proper installation and training, material selection, secure sealing techniques, thorough testing and quality control, and proactive measures are crucial.
#checkout our other website http://indiavalves.co.in