Understanding actuator valve technology
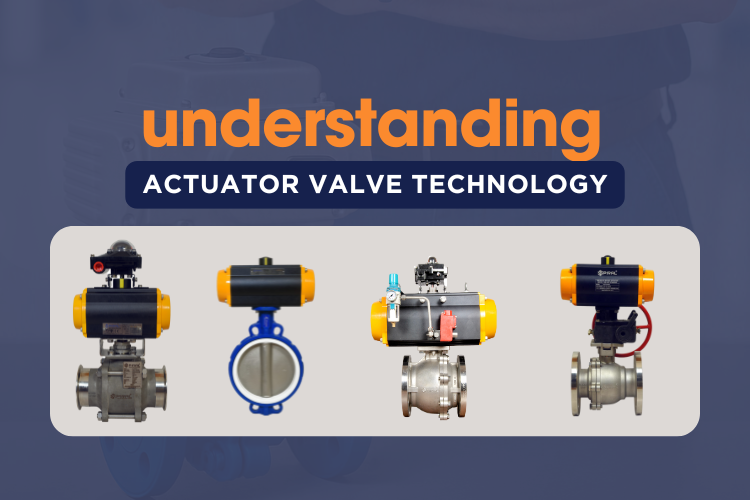
Have you ever wondered how massive industrial processes are controlled with such precision? The secret lies in a small but mighty device: the actuator valve. These unsung heroes of the industrial world are responsible for regulating everything from water flow in treatment plants to chemical processes in refineries.
But what exactly is an actuator valve, and why is it so crucial? Whether you’re an industry professional or simply curious about the technology that powers our modern world, understanding actuator valve technology is key to grasping the intricacies of industrial automation. From pneumatic to hydraulic, electric to manual, these valves come in various types, each with its own unique advantages and applications.
In this comprehensive guide, we’ll dive deep into the world of actuator valves. We’ll explore their types, how they work, and their diverse applications across industries. You’ll learn how to choose the right actuator valve for your needs and even pick up some maintenance tips along the way. So, let’s embark on this journey to unravel the mysteries of actuator valve technology and discover how these small components make a big impact in our daily lives.
Introduction
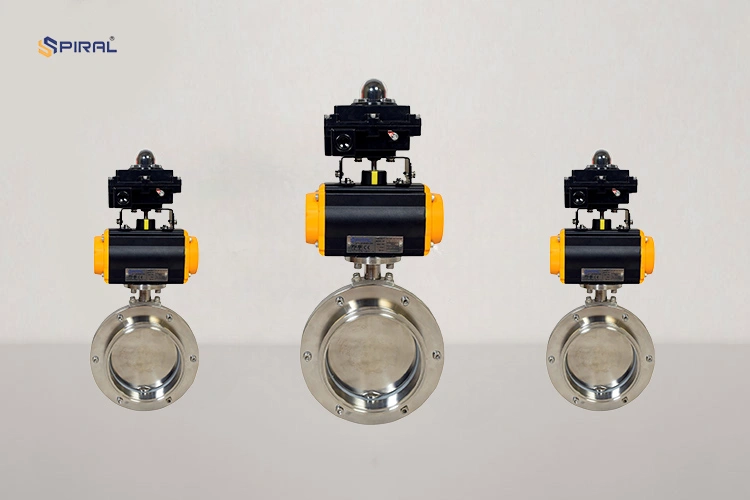
A. Brief overview of what actuator valves are
Actuator valves are sophisticated devices that combine the functionality of a valve with an automated control mechanism. These components play a crucial role in regulating the flow of liquids, gases, or slurries in various industrial processes. At their core, actuator valves consist of two main parts: the valve itself and the actuator, which provides the motive force to open, close, or modulate the valve’s position.
B. Why they matter in modern industrial systems
Actuator valves are indispensable in modern industrial systems for several reasons:
- Precision control
- Remote operation
- Increased safety
- Energy efficiency
- Process automation
Benefit | Description |
---|---|
Precision control | Allows for exact regulation of flow rates |
Remote operation | Enables control from a centralized location |
Increased safety | Reduces human interaction with hazardous materials |
Energy efficiency | Optimizes resource usage in industrial processes |
Process automation | Facilitates seamless integration with control systems |
C. Mention your expertise as a manufacturer
As a leading manufacturer of actuator valve technology, we have been at the forefront of innovation in this field for over two decades. Our extensive experience has allowed us to develop cutting-edge solutions that cater to the diverse needs of industries ranging from oil and gas to water treatment and chemical processing. Our commitment to quality and continuous improvement ensures that our actuator valves meet the highest standards of performance and reliability.
What is an Actuator Valve?
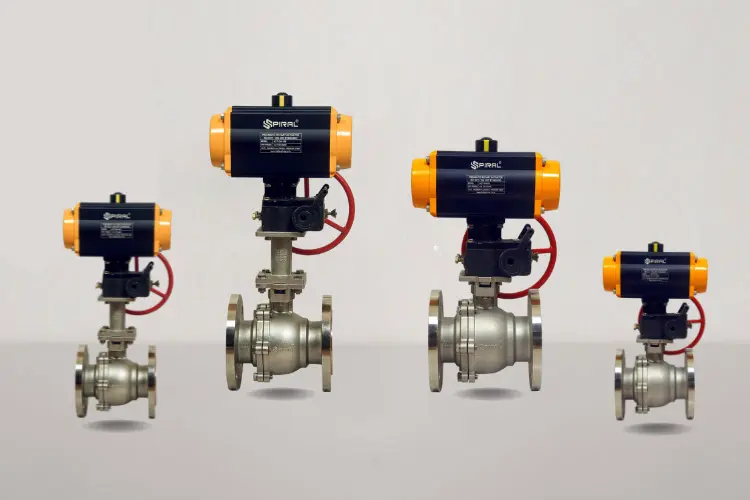
Definition and function
An actuator valve is a critical component in fluid control systems, combining a valve with an actuator mechanism. This device regulates the flow of liquids, gases, or slurries by automatically opening, closing, or modulating the valve position. The actuator, powered by various energy sources, provides the necessary force to operate the valve, ensuring precise control over fluid flow.
Role in automating valve control
Actuator valves play a pivotal role in automating industrial processes by:
- Enhancing precision and consistency
- Reducing human intervention
- Enabling remote operation
- Improving safety in hazardous environments
- Facilitating real-time process adjustments
These benefits make actuator valves indispensable in modern industrial settings, where efficiency and reliability are paramount.
Manual vs automated valves comparison
Feature | Manual Valves | Automated Valves |
---|---|---|
Operation | Human intervention required | Remotely controlled |
Precision | Variable, depends on operator | Highly accurate |
Response time | Slower | Faster |
Consistency | May vary | Highly consistent |
Monitoring | Limited | Real-time data available |
Maintenance | Generally lower | May require specialized maintenance |
Initial cost | Lower | Higher |
Long-term efficiency | Lower | Higher |
Automated valves offer significant advantages in terms of precision, consistency, and efficiency. However, manual valves may still be preferred in certain applications where simplicity and lower initial costs are prioritized. The choice between manual and automated valves depends on the specific requirements of the application, including factors such as process complexity, safety considerations, and operational demands.
Types of Actuators Used in Valves
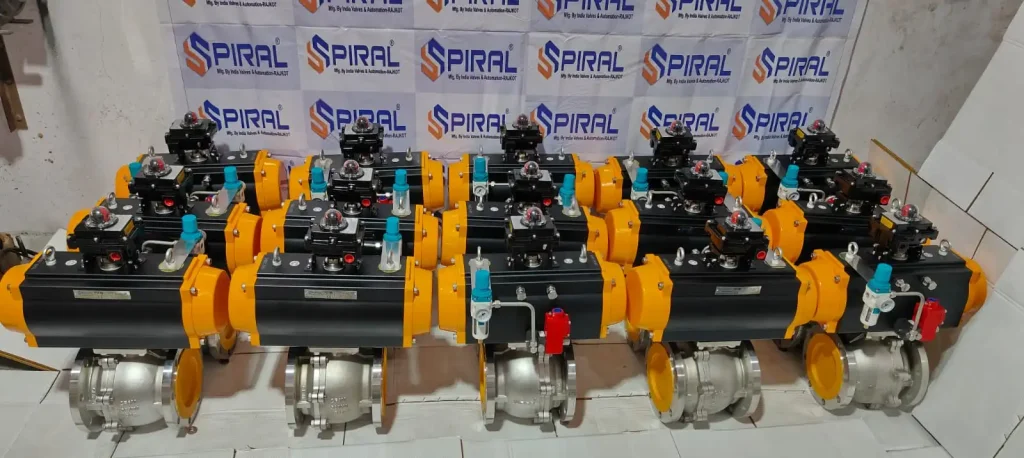
Electric actuators
Electric actuators are popular in valve control systems due to their precision and reliability. They use an electric motor to convert electrical energy into mechanical motion, operating the valve. These actuators are ideal for applications requiring precise control and are often used in industries like water treatment, HVAC, and power generation.
- Key features:
- High accuracy and repeatability
- Easy integration with digital control systems
- Low maintenance requirements
- Suitable for both indoor and outdoor applications
Pneumatic actuators
Pneumatic actuators utilize compressed air to generate mechanical force. They are known for their simplicity, fast response times, and ability to operate in hazardous environments. These actuators are commonly found in process industries, oil and gas, and manufacturing plants.
- Advantages:
- Cost-effective for certain applications
- Intrinsically safe for explosive environments
- Rapid cycling capabilities
- Can provide high force output
Hydraulic actuators
Hydraulic actuators use pressurized fluid to create mechanical force. They excel in applications requiring high force output and are often used in heavy-duty industrial settings, such as mining, construction, and large-scale manufacturing.
- Key characteristics:
- Capable of generating extremely high forces
- Smooth and precise operation
- Self-cooling properties
- Suitable for continuous duty cycles
Comparison chart of features, pros & cons
Feature | Electric | Pneumatic | Hydraulic |
---|---|---|---|
Power source | Electricity | Compressed air | Pressurized fluid |
Force output | Medium | Medium to High | Very High |
Speed | Moderate | Fast | Variable |
Precision | High | Medium | High |
Maintenance | Low | Medium | High |
Cost | High initial, low operating | Medium initial, medium operating | High initial, high operating |
Environmental concerns | Low | Low (air leaks) | Medium (fluid leaks) |
Now that we’ve explored the different types of actuators used in valves, let’s delve into how these actuator valves actually work in practice.
How Actuator Valves Work
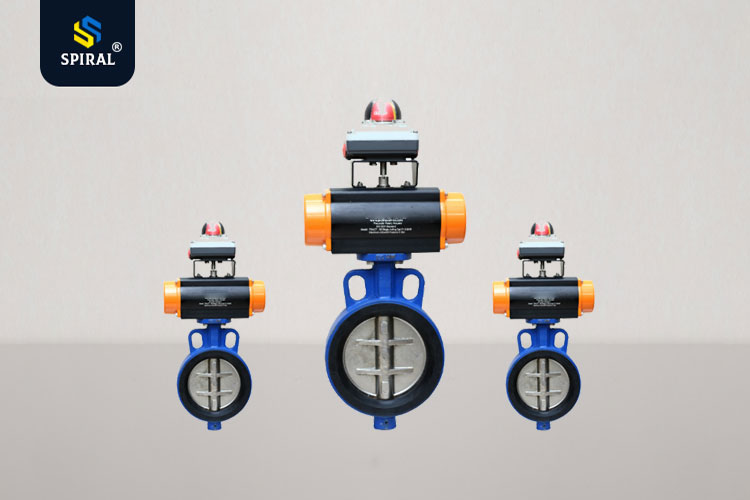
When it comes to automation in flow control systems, actuator valves are the unsung heroes. But how exactly do they work? Let’s pull back the curtain and take a closer look at how these vital components convert signals into precise, reliable motion—keeping industrial systems running smoothly
From Signal to Movement: The Core Process
Actuator valves follow a simple but powerful logic: they receive a signal, generate motion, and control a valve accordingly. Here’s a step-by-step walkthrough of how that happens:
- Input Signal
The process begins when a control system sends a signal—usually electric, pneumatic, or hydraulic—to the actuator. - Energy Conversion
The actuator takes this energy and converts it into mechanical force, either rotational or linear, depending on the application. - Valve Operation
This force is used to move the valve—opening, closing, or adjusting it—to regulate the flow of a substance (liquid, gas, or steam). - Feedback (in automated systems)
Some systems include feedback mechanisms that confirm valve position and send real-time data back to the controller for further adjustments.
Motion Types: Rotary vs. Linear
Different industrial valve types require different kinds of motion, and actuators are designed accordingly:
- Rotary Actuators
These rotate the valve stem—common in ball, plug, and butterfly valves. They’re compact and ideal for quick, quarter-turn operations. - Linear Actuators
These move the valve stem up and down—perfect for globe, gate, and diaphragm valves that need throttling or slow, steady movement.
Understanding which type of motion your system needs is critical to choosing the right actuator.
Control You Can Count On
What makes actuator valves such an essential part of industrial operations? They bring:
- Consistency – Every movement is repeatable and reliable, ensuring steady system performance.
- Speed – Fast response times for critical adjustments.
- Safety – Reduced need for manual operation in hazardous or remote areas.
- Precision – Fine control for systems that require exact flow regulation.
Why It Matters
Whether you’re managing a wastewater treatment plant or overseeing a high-pressure gas pipeline, you need systems that react fast and accurately. Actuator valves take human error out of the equation and give you the confidence to scale and automate complex processes without compromise.
At the end of the day, they’re not just moving parts—they’re essential decision-makers in your system’s performance.
Applications in Various Industries
Actuator valves aren’t limited to one sector—they’re everywhere. From managing high-pressure steam in power plants to maintaining clean water in municipal systems, these dynamic tools play a critical role across a wide range of industries. Let’s explore where and how actuator valve technology makes a real-world impact.
1. Oil & Gas: Controlling High-Stakes Flow
In the oil and gas sector, reliability and safety are non-negotiable. Actuator valves are used to:
- Automatically open or close pipeline valves to manage pressure
- Control blowout preventers and emergency shut-off systems
- Integrate with SCADA systems for remote monitoring and control
With the volatile nature of this industry, actuators provide quick-response performance and reduce the risk of hazardous manual operations.
2. Water and Wastewater Management: Smart, Clean Flow
Municipal and industrial water systems depend on actuator valves for:
- Regulating water distribution
- Managing flow in treatment facilities
- Automating chemical dosing and filtration systems
Because these systems often span wide geographic areas, remote-controlled industrial valves are crucial for efficient operations and leak prevention.
3. Power Generation: Pressure and Precision
In energy plants—whether nuclear, fossil fuel, or renewable—flow regulation is key. Actuator valves are used to:
- Handle steam, gas, and water flow through turbines and boilers
- Ensure stable pressure levels during generation cycles
- Automate safety and release mechanisms
Their precision keeps energy systems efficient while protecting against dangerous pressure surges.
4. Manufacturing & Process Automation: Streamlined Systems
From food and beverage to pharmaceuticals and chemicals, actuator valves support:
- Batch processing with precise fluid control
- Clean-in-place (CIP) operations
- Integration with automated production lines
In this environment, downtime is costly. Actuator valves help streamline production while meeting strict compliance and hygiene standards.
5. HVAC and Building Systems: Comfort Meets Control
In commercial and industrial buildings, actuator valves regulate:
- Heating and cooling systems
- Water and air pressure in ventilation
- Fire suppression system flow
These systems benefit from actuators because they offer automated adjustments, improve energy efficiency, and enhance occupant comfort.
Choosing the Right Actuator Valve
Choosing the correct actuator valve is more than simply a technical decision; it’s a strategic one that affects your system’s efficiency, safety, and maintenance costs. The procedure begins with an understanding of your individual application. Do you manage high-pressure steam, regulate chemical flow, or handle water distribution? Each environment has unique requirements in terms of temperature, pressure, flow rate, and safety norms. Matching those requirements to the appropriate actuator type—electric, pneumatic, or hydraulic—is critical for attaining long-term dependability and performance.
In addition to the application, you should think about the kind of valve and movement that are required. Whereas linear actuators work better with gate or globe valves that need precision, vertical movement, rotary actuators are best suited for quarter-turn valves like ball or butterfly valves. Choosing the best actuator also involves considerations of torque, operating speed, and response time. Additionally, don’t forget about system compatibility; whether your actuator is digital, manual, or part of a broader SCADA network, it must operate flawlessly with your control configuration.
Your decision is also influenced by environmental circumstances. Will the actuator be used in an explosive zone, outside, or in a corrosive environment? System performance can be made or broken by features like explosion-proof ratings, fail-safe alternatives, and waterproof housings. In the end, selecting the ideal actuator valve requires striking a balance between control, longevity, and functionality to make sure your industrial valve system operates smoothly now and scales with ease tomorrow.
Maintenance and Troubleshooting
Even the best actuator valve systems need a little TLC from time to time. Maintenance doesn’t just prevent failures—it gets you the most out of your investment. Think of it like getting a check up before you get sick. Simple things like checking seals, looking for leaks and testing actuation can go a long way in extending the life of the actuator and the valve it controls.
When things don’t go as planned troubleshooting can feel overwhelming—but it doesn’t have to be. Most issues are easy to spot once you know what to look for. Is the valve not moving? You might have a power supply issue or a stuck actuator. Getting unusual flow readings? Maybe the actuator isn’t calibrated or there’s a blockage in the valve itself. Start with the basics—verify signals, check connections and isolate the issue step by step.
Keeping a maintenance log and a simple troubleshooting guide can save you hours of guessing later. And don’t underestimate the power of manufacturer support or system diagnostics—many modern actuators have built in feedback or error codes to help you find the problem faster. A little proactive maintenance keeps your systems running smooth, prevents downtime and gives you peace of mind knowing everything is under control.
Conclusion
Actuator valve technology may not always be visible, but it’s working behind the scenes to keep critical systems flowing safely, efficiently, and reliably. Whether it’s opening a valve deep in a remote oil field or fine-tuning water flow in a municipal plant, the role of the actuator is central to modern automation and control. By understanding how these components work, where they’re used, and how to choose and maintain them, you’re better equipped to make smarter, more confident decisions.
As industries continue to lean into intelligent systems and connected operations, actuator valves will only become more essential. Investing in the right technology—and taking care of it—isn’t just about system performance. It’s about future-proofing your operation. So, whether you’re upgrading an existing setup or designing something from scratch, remember: behind every well-regulated industrial valve, there’s a powerful actuator making it happen.